Các nhà nghiên cứu và sản xuất phụ tùng ô tô Nhật Bản đã chế tạo thành công loại vật liệu từ bột giấy, trọng lượng chỉ bằng 1/5 thép nhưng rắn chắc gấp 5 lần.
Loại vật liệu đó chính là sợi nano cellulose (cellulose nanofiber), trong khoảng 10 năm tới nó có thể thay thế cho thép. Tuy nhiên, bên cạnh đó là sự cạnh tranh mạnh mẽ của vật liệu carbon, sợi nano cellulose sẽ còn rất lâu mới được thương mại hóa.
Khi xu hướng sử dụng xe điện dần trở thành chủ đạo trong tương lai, các nhà sản xuất luôn hướng đến các loại vật liệu nhẹ, làm giảm trọng lượng tổng thể của xe - đồng nghĩa với việc pin, động cơ sẽ bớt được sức tải, do đó tiết kiệm được nhiều năng lượng hơn.
Masanori Matsushiro, giám đốc dự án thiết kế thân xe của Toyota Motor Corp cho biết:
"Giảm trọng lượng thân xe là một vấn đề mà chúng tôi luôn phải đối mặt. Tuy nhiên, cũng phải giải quyết được một vấn đề khác là chi phí sản xuất đắt đỏ trước khi có thể đưa vật liệu mới nhẹ hơn vào sản xuất đại trà."
Các nhà nghiên cứu tại Đại học Kyoto đang hợp tác với Denso (nhà cung cấp phụ tùng lớn nhất cho Toyota) và tập đoàn DaikyoNishikawa (đối tác với Toyota Motor và Mazda Motor) để cho ra mắt loại vật liệu làm từ chất dẻo kết hợp với sợi nano cellulose.
Sợi nano cellulose đã được ứng dụng vào nhiều sản phẩm khác nhau, từ mực in cho đến màn hình trong suốt.
Tuy nhiên, để làm phụ tùng xe ô tô vẫn cần rất nhiều giai đoạn nghiên cứu và thử nghiệm. Sử dụng "quy trình Kyoto" (Kyoto Process) - gỗ được xử lý hóa học, pha trộn với chất dẻo, điều này giúp cắt giảm 1/5 chi phí sản xuất so với các quy trình khác.
Hiroaki Yano, Giáo sư Đại học Kyoto chia sẻ với Reuters: “Đây là quy trình sản xuất nano cellulose với chi phí thấp nhưng cho hiệu quả cao nhất. Đó là lý do vì sao chúng tôi muốn đưa nó vào sản xuất phụ tùng ôtô và máy bay.”
Các nhà nghiên cứu cùng các nhà cung cấp phụ tùng ôtô hiện đang phát triển một mẫu xe sử dụng các bộ phận từ nano cellulose, dự kiến sẽ hoàn thành vào năm 2020.
Yukihiko Ishino, phát ngôn viên của tập đoàn DaikyoNishikawa, cho biết: “Chúng tôi đang thử sử dụng chất dẻo để thay thế cho thép. Chúng tôi kỳ vọng rằng nano cellulose sẽ đáp ứng được nhiều tiêu chuẩn khắt khe.”
Các nhà sản xuất ô tô còn sử dụng các vật liệu nhẹ thay thế khác. BMW sử dụng sợi carbon gia cường kết cấu (CFRP) trên dòng xe điện i3 cũng như 7 series của mình, trong khi thép độ bền cao (high-tensile steel) và hợp kim nhôm hiện là lựa chọn tối ưu nhất được sử dụng rộng rãi vì chúng rẻ và có thể tái chế.
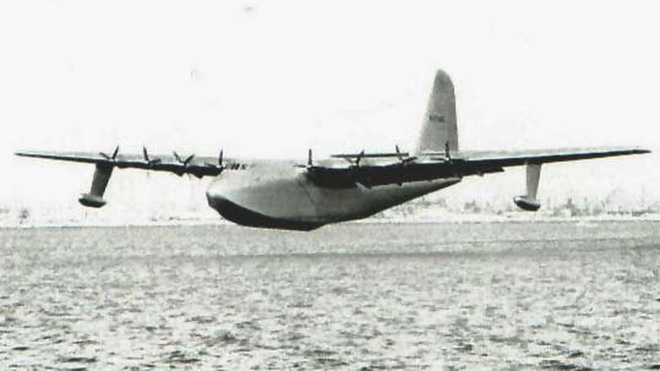
Spruce Goose - chiếc máy bay gần như làm hoàn toàn bằng gỗ của tỷ phú Mỹ Howard Hughes
Yano cho biết ông lấy cảm hứng từ bức ảnh Spruce Goose, biệt danh của chiếc máy bay chở hàng gần như bằng gỗ hoàn toàn xuất hiện vào năm 1947 của tỷ phú Mỹ Howard Hughes. Nó là chiếc máy bay lớn nhất thế giới khi ấy.
“Nếu Howard Hughes có thể dùng gỗ chế tạo ra một chiếc máy bay không lồ, thì tại sao lại không thể sử dụng gổ để tạo ra một vật liệu bền như thép?”
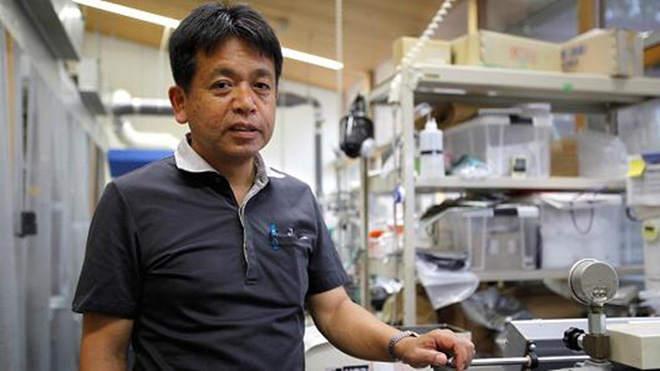
Giáo sư Hiroyuki Yano đến từ Đại học Kyoto, một trong những người đặt kỳ vọng vào sợi nano cellulo
Hiện tại, chi phí sản xuất 1kg nano cellulose rơi vào khoảng 9 USD. Yano và đội ngũ của ông dự định sẽ giảm một nửa chi phí vào năm 2030, trở thành loại vật liệu có sức cạnh tranh với thép, các loại hợp kim nhôm (2 USD/kg). Nhiều chuyên gia cho rằng, giá sợi carbon sẽ giảm xuống 10 USD/kg vào năm 2025.
Giới phân tích cho rằng thép độ bền cao và hợp kim nhôm sẽ ngày càng phổ biến trong nhiều năm tới, khi nhà sản xuất phụ tùng phải thay đổi dây chuyền sản xuất, tìm cách để đưa vật liệu mới như nano cellulose vào các bộ phận của ôtô.
Nguồn: Reuters